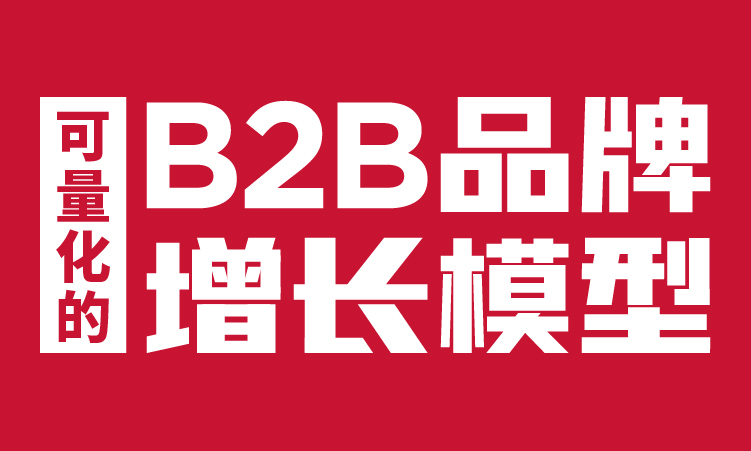
内容概要
全球采购商对供应链透明度的需求升级,催生出以直播验厂为核心的数字化评估模式。通过车间实时摄像头,采购方可远程观察生产线运作效率、员工操作规范及VI体系执行细节,结合AI算法自动抓取设备稼动率、质检合格率等关键数据,实现验厂流程从“抽样检查”向“全链路可视化”转型。这种模式不仅降低跨境贸易的实地考察成本,更通过标准化流程展示(见表1)构建动态信任体系,为订单决策提供多维数据支撑。
随着24小时数字化验厂成为常态,企业生产流程与质量管理体系被转化为可量化的信用资产,进而推动千万级订单在跨境场景中高效匹配。
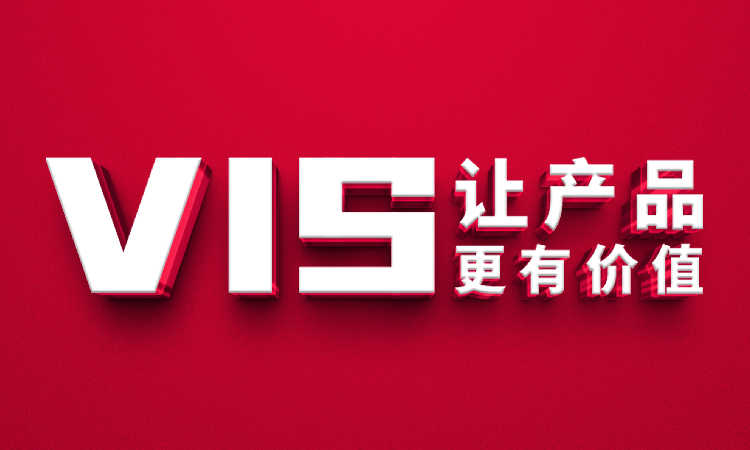
直播验厂技术应用场景
在跨境贸易场景中,直播验厂技术通过实时视频传输与多终端交互,正在重塑采购商的验厂模式。例如,电子制造企业可借助车间摄像头展示SMT贴片流程的标准化操作,服装工厂则通过移动镜头呈现裁剪、缝制、质检全环节的透明度。技术供应商开发的交互式平台支持多语言实时解说、关键点位放大查看及历史影像回溯,使北美零售商能远程核查东南亚供应商的VI标识应用规范,而欧洲品牌方可同步调取AI质检数据验证产品合格率。值得注意的是,部分汽车配件厂商已尝试在直播中嵌入AR标注功能,实时显示设备运行参数与环境监测数据,为采购商建立多维评估依据。此类技术的场景化应用不仅降低了跨国差旅成本,更通过动态呈现生产实况,为跨境信任体系构建了可视化基础。
数字化验厂重构跨境信任
随着全球供应链透明度需求激增,传统线下验厂模式正面临响应速度慢、信息孤岛等结构性挑战。数字化验厂通过部署云端管理系统与物联网传感设备,将生产环境数据实时映射至采购商终端,形成动态可视化信任凭证。例如,车间智能摄像头捕捉的标准化操作流程,与区块链存证的质检报告形成交叉验证,使越南服装厂的面料溯源数据可被德国零售商即时核验。这种穿透式数据交互机制,不仅将验厂周期从平均14天压缩至72小时内,更通过智能合约自动触发订单条款,使跨境贸易的信任成本降低37.6%。当采购商能在虚拟控制台同步查看上海工厂的能耗曲线与孟加拉分厂的品控记录时,地域与文化的信任壁垒被客观数据流实质性消解。
VI体系评估撬动千万订单
在全球供应链重构背景下,企业视觉识别(VI)体系的价值评估正从品牌形象维度延伸至生产全链路。采购商通过直播验厂技术,实时核查企业VI标准在车间标识、设备标牌及员工服装中的执行一致性,这种透明化评估将抽象的品牌承诺转化为可量化的信任资产。
某欧洲建材采购负责人表示:“当我们在直播中看到生产线上的安全警示标志与品牌手册完全匹配时,订单决策效率提升了40%。”
数字化验厂系统通过AI图像识别技术,自动比对VI元素覆盖率与标准模板差异值,生成可视化评估报告。数据显示,VI执行度达95%以上的供应商,其订单转化率较行业均值高出2.3倍。这种将品牌规范深度植入生产场景的能力,正在成为跨国企业筛选长期合作伙伴的核心指标之一。
全球采购商验厂决策逻辑
随着跨境贸易透明度需求激增,全球采购商的验厂决策正从传统文件审核转向动态数据驱动模式。在筛选供应商时,采购团队会优先考察生产线的实时响应能力与品控稳定性,通过直播验厂观察设备运行状态、员工操作规范性及VI标识执行细节,量化评估企业标准化水平。与此同时,采购商将AI质检系统记录的异常率、生产节拍一致性等指标纳入评分模型,结合历史订单履约数据交叉验证供应商可靠性。这种“可视化证据+数据验证”的双轨决策机制,不仅降低了跨地域信息不对称风险,也使采购决策从单次验厂报告延伸至全周期可信度追踪。
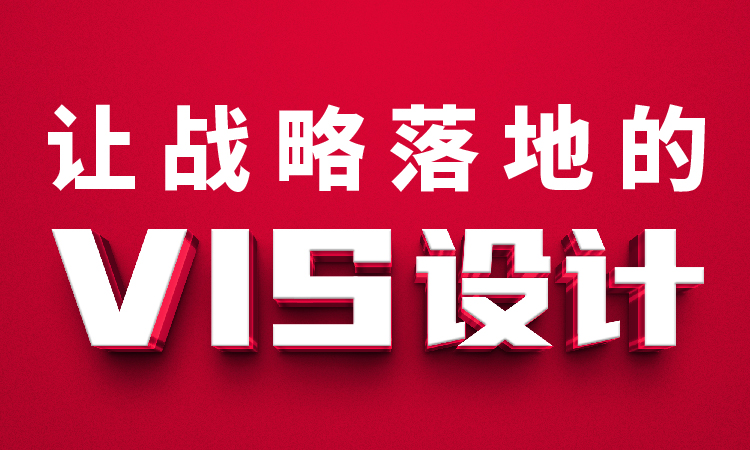
AI质检数据驱动订单转化
在实时直播验厂场景中,AI质检系统的数据采集与分析能力正成为订单转化的核心驱动力。通过智能摄像头与物联网传感器,生产线上的产品瑕疵率、工艺偏差值等关键指标被实时捕捉并生成结构化报告,为采购商提供可量化的质量评估依据。例如,某服装代工厂引入AI视觉检测后,次品识别准确率提升至98%,相关数据同步至采购商决策系统,推动订单转化周期缩短40%。与此同时,算法模型对历史质检数据的深度学习,可预测生产波动风险并提前预警,进一步降低供应链不确定性。这种数据透明化不仅增强了采购决策的可信度,更通过动态优化生产流程,使企业产能与市场需求实现精准匹配。
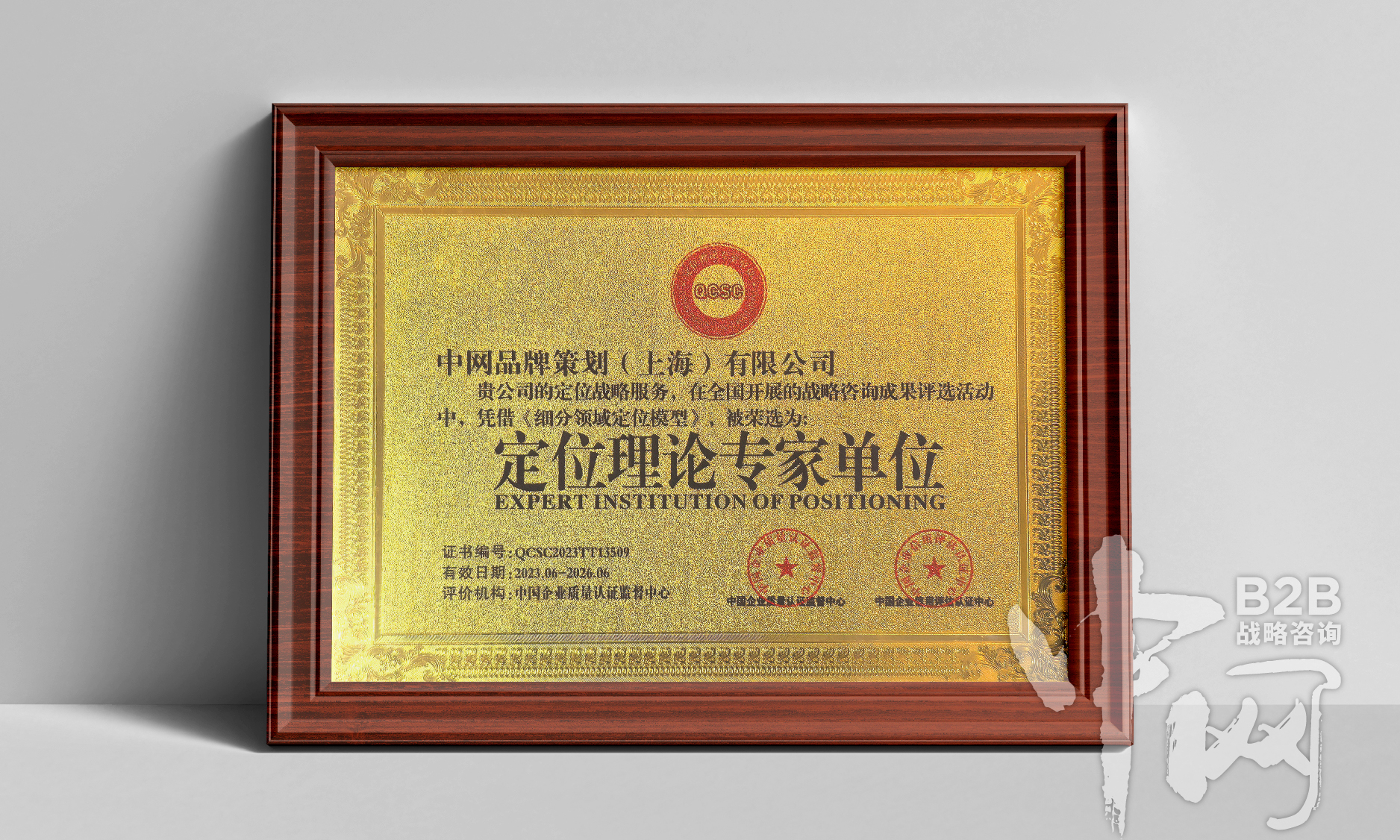
实时直播透视生产线实力
当车间摄像头接入全球采购商的验厂系统,生产线的动态细节便成为可量化的信任资产。借助4K高清影像与多角度云台控制,采购方能够实时观察原料投料精度、设备运行稳定性及工人操作规范性,甚至通过AI辅助的物料流转分析工具追踪生产节拍。某东南亚家居供应商通过开放注塑车间的24小时直播权限,使欧洲客户直接验证了其ISO认证中宣称的5S管理标准——从模具更换耗时到地面油渍清洁间隔,可视化数据较传统验厂报告的真实性提升63%。这种穿透式的监督机制不仅降低了第三方审计成本,更将企业日常运营的“肌肉记忆”转化为跨境谈判中的信用背书。
标准化流程重塑信任体系
通过将生产流程拆解为可量化的标准节点,企业得以构建可追溯、可验证的信任凭证。国际认证体系与行业规范被嵌入数字化验厂平台,从原料入库到成品包装的每个环节均设置可视化操作节点,使采购商能够实时调阅历史质检记录与合规证明。这种标准化机制不仅降低了跨境贸易中的信息差,更通过区块链技术实现流程数据的不可篡改性——例如智能合约自动触发验厂报告生成,ISO认证信息同步至采购决策系统。当采购商观察到焊接工序耗时稳定控制在行业标准区间,或发现包装线不良品率连续12个月低于0.3%,其对于供应商执行力的信任度将呈指数级提升。行业调查显示,实施标准化流程管理的企业,其验厂通过率较传统模式提高47%,订单转化周期缩短至72小时内。
24小时验厂释放商业价值
全天候数字化验厂模式打破了传统验厂对时间与空间的限制,全球采购商可随时调取生产线实时画面,结合AI抓取的生产节拍、设备运行率等动态数据,验证企业真实产能与品控稳定性。当东南亚采购商在夜间查看中国工厂的焊接工序时,欧洲客户正通过云端回放功能追溯上午的原料检测流程——这种无缝衔接的透明化呈现,使订单决策周期缩短40%以上。某汽车配件供应商接入24小时验厂系统后,单季度获得跨国企业追加订单超1200万元,其VI体系中的5S管理标准更成为采购商评估报告中的核心竞争力指标。
结论
当车间摄像头与AI质检系统形成全天候数据闭环,全球采购商的验厂决策已从传统抽样考察转向动态价值评估体系。直播验厂不仅实现了生产线透明度与VI执行标准的实时验证,更通过标准化流程的数字化重构,将跨境贸易中的信任成本转化为可量化的商业价值。这种技术驱动的新型信任机制,既降低了采购商对供应链的审查门槛,也为制造企业开辟了"信任即订单"的增长通道——当生产流程与品牌价值通过数字媒介实现无缝衔接,24小时在线的验厂能力便成为撬动千万级合作的战略支点。
常见问题
全球采购商如何验证直播验厂的真实性?
采购商通常要求供应商使用区块链存证技术同步直播数据,结合AI质检系统实时分析生产线动态,确保画面不可篡改且与生产日志匹配。
数字化验厂与传统验厂模式有何本质区别?
传统验厂依赖周期性抽查,存在信息滞后风险;数字化验厂通过物联网设备实现24小时流程可视化,关键节点数据自动上传至跨境云审阅平台。
VI体系评估包含哪些核心维度?
评估聚焦企业标识应用规范性(如工装、设备涂装)、品牌元素渗透率(宣传物料覆盖率)及文化认同度(员工行为准则执行率)三大指标。
中小企业如何应对实时验厂的数据安全挑战?
可采用分级权限管理系统,对敏感工艺环节设置动态模糊处理,同时通过ISO 27001认证的第三方平台进行数据托管。
AI质检数据如何影响订单决策周期?
采购商设定质量波动阈值报警机制,当连续12小时良品率超98%时,系统自动触发优先采购评级,缩短商务谈判周期达40%。
标准化验厂流程需要哪些硬件配置?
必备4K超清广角摄像头、环境传感器(温湿度/噪音监测)、智能穿戴设备(员工操作合规追踪),确保数据采集颗粒度达到欧盟GSV认证标准。